Prefabrication techniques have been used in commercial construction for a long time and are becoming increasingly more common in residential construction as well. Technology has also made prefabricated products not only more attractive, but more energy efficient and built to last. If you’re a builder or investor, prefabrication can benefit you in many ways, the most significant being cost and time savings. Another advantage of prefabrication is that it can be environmentally friendly as it creates less material waste. Below, we’ve outlined some of these benefits in greater detail.
Prefabrication reduces construction costs in a couple of ways. Firstly, because everything is made to measure offsite in precise, controlled factory settings, what arrives on your construction site is exactly what you need, with no wasted or excess materials. With prefabrication, materials need not be cut from larger pieces, resulting in unusable scraps and wasted money. In many cases, prefabricated sections of a home are able to account for plumbing and electrical requirements and have them built in exactly the right spots with exactly the right amount of material.
The website New York Engineers gives an excellent example of this: “Materials that come in predetermined shapes or sizes must often be cut before installation, and leftover pieces are frequently wasted. For example, electrical conduit is purchased in 10’ pipes, and a circuit that measures 28’ will leave you with 2’ of conduit. Unless another circuit requires just that amount, a piece of conduit is wasted.”
Another way prefabrication can reduce cost is by reducing the amount of labor needed on site. For example, entire sections of a home can be constructed in a factory using methods such as panelized construction - a system of precision cut panels (which sometimes already include windows and doors) that are simply assembled onsite, reducing the number of tradespeople needed and the amount of time required to build.
Construction technology such as Building Information Modeling also reduces guesswork, man power, and man hours. According to eSub Construction Software, “BIM combines technology and construction to help contractors and companies visualize the scope of the project. The integration of technology and construction can visualize the cost and material differences, which can, therefore, reduce construction material costs and wasted labor hours.”
And the green benefits of prefabrication go beyond reduced waste. In addition to creating only the precise numbers and amounts of materials as mentioned above, many prefabricated materials are extremely energy efficient as well, one excellent example being structured insulated panels or SIP’s. A type of panelized construction, SIP’s are built with a layer of insulating foam in between them, then brought to the building site ready to be put in place. They are also very lightweight, making them easy to work with.
The bottom line is, prefabricated construction methods allow you to save time, save money, and reduce waste. This allows you, the investor, to scale up and focus on multiple projects at once, helping your business and your profits grow.
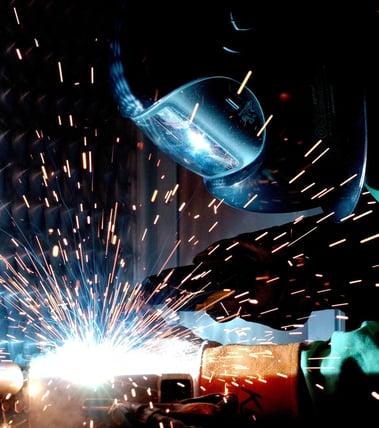
Recent Posts
- Spec Construction Loans: A Spec Line of Credit Is Worth the Paperwork
- Spec Homes and Pre-Sale Homes: The Relative Benefits for a Spec Builder
- How a Lender Sees Spec Construction Success: Insights for the Investor Builder
- How Is a Spec House Different From Other Kinds of House Construction?
- How a Private Lender Compares to a Bank Lender for a Spec House Construction Loan